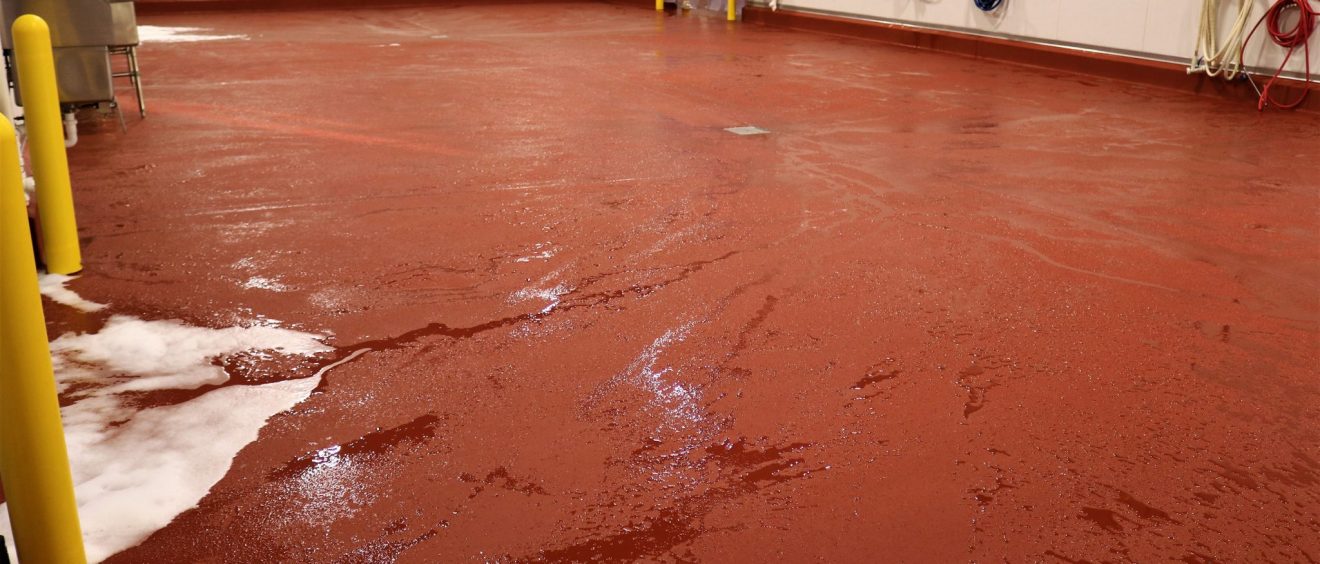
Correcting a Failed Floor in NW Salsa Facility
Installing new flooring is a significant investment for any business, one whose costs can increase exponentially with improper installation or poor product choice. Our client, a Northwest area food processor, found themselves facing these costly repairs when the initial flooring/ an inexperienced contractor installed an epoxy flooring system in their new production facility.
Almost immediately our client began seeing signs of floor failure; delamination appeared as layers of the epoxy coating became unbonded with the substrate below. Cracks in the brittle coating appeared in high traffic areas, creating an unsafe environment for food production. After several failed repair attempts, our client began the legal process with the flooring contractor, and Poe Construction turned to us for the re-installation. Upon inspection it was clear that the floor had failed primarily due to product selection and inexperience; the previous flooring contractor had selected an epoxy system, a product unfit for our client’s extreme environment and they failed to perform sufficient surface preparation prior to installation.
While epoxy floor coatings can create a seamless and non-slip environment, they are better suited in industrial and commercial settings other than food and beverage production. These facilities regularly use extremely hot water to washdown their production areas, and epoxies do not hold up well to this repeated exposure to high temperatures. While epoxies are heat resistant, in that they will not melt or burn below a specific point, when heated above a certain temperature (typically 140-160 degrees Fahrenheit), they become pliable and expand. Once cooled, they contract and become brittle. This process is called thermal cycling, and the repeated expansion and contraction of the epoxy weakens its bond with the substrate below, leading to bucking of the coating, delamination, and eventual failure like that which our client saw in their floor.
Based on the condition of the concrete below the epoxy, it was clear that the previous contractor did not perform adequate surface preparation prior to installation. Proper surface prep is crucial to any successful floor installation, particularly when working with epoxy. Epoxies adhere to concrete at a specific Concrete Surface Profile (CSP), achieved mechanically through grinding, scarifying, or shot blasting. If a contractor does not use the proper equipment or method of preparation to achieve the CSP, the coating is destined for failure.
Our Process
We knew that we needed to completely remove the existing failed flooring and install a product better suited for the food and beverage industry, choosing BASF’s Ucrete BC6 seamless flooring system. We recommend Ucrete and similar urethane mortar systems for food production environments because they are USDA compliant, long-lasting, extremely durable, and resistant to abrasions and chemicals. Unlike epoxy, urethane concrete is made of a cementitious formula designed to withstand thermal cycling, so that it remains bonded even after repeated exposure to high temperatures. Ucrete is also formulated to chemically react with the substrate, providing additional adhesion. We’ve installed Ucrete in many food production facilities and have seen that with proper maintenance, these floors can last upwards of 20 years.
Because food production is 24 hour business, we worked with Poe and our client to create a three-phase schedule that would allow our client’s facility to remain operational. Poe Construction installed full height barriers to separate the working facility from our construction, and we used products with low VOCs and air handling equipment to minimize airborne contaminants.
We removed the existing flooring using our Terminator T 2000 Floor Scraper and used a Blastrack BMP 4000 and 20” Shot Blaster to prepare the floor to a Concrete Surface Profile of 4, the correct profile for Ucrete to bond with the concrete. The shot blaster prepares the concrete by propelling steel shot centrifugally at a high velocity, stripping off any dirt or paint and leaving a roughened texture. It produces very little airborne dust, which was vital in our clients enclosed facility.
Next, we installed Ucrete BC6. BC6 is rolled onto the concrete to a thickness between ¼ and 3/8 inch, and troweled onto the edges. Ucrete WR RG cove base was applied 18” vertically as additional protection to the walls. These cured over-night and we were able to apply the topcoat the next morning. We used a DP topcoat, a solvent free, heavy duty polyurethane resin topcoat that provides additional temperature and chemical resistance.
Once the topcoat cured, joints were cut into the Ucrete coating to match the control joints in the concrete slab below. Concrete naturally expands and contracts, and control joints are used to control this movement and minimize random cracking. If joints are not matched in the coating on top, the concrete below will move and compromise the flooring. We filled the joints cut in the ucrete with Metzger McGuire RS88, a semi-rigid polyurea joint filler made for high-traffic areas. This allows the concrete to move naturally, without allowing moisture or bacteria to enter the joints.
Project Completion
The completed floor was extremely successful, though there were various challenges that we faced during this project. Because of the outdoor temperature, we needed to provide heating to our workspace. Because of our client’s operational needs, we performed our work in three-phases under a strict timeline. Through careful planning and caution, we were able to deliver each phase back to the client ahead of schedule.
Ultimately, the success of the project came down to our knowledge and product selection, having the proper equipment for the job, the skills and workmanship of our experienced crew, and a successful partnership with a general contractor, Poe Construction, who provided support for our needs throughout the project. For clients like ours who find themselves facing the unfortunate situation of a failed floor, finding the right contractor is top priority. With over 30 years of specialized experience, we are confident in our ability to offer cost-effective and long-lasting options to every business.